年產(chǎn)15000噸嬰兒配方粉工廠設(shè)計(jì)模具專業(yè)畢業(yè)論文
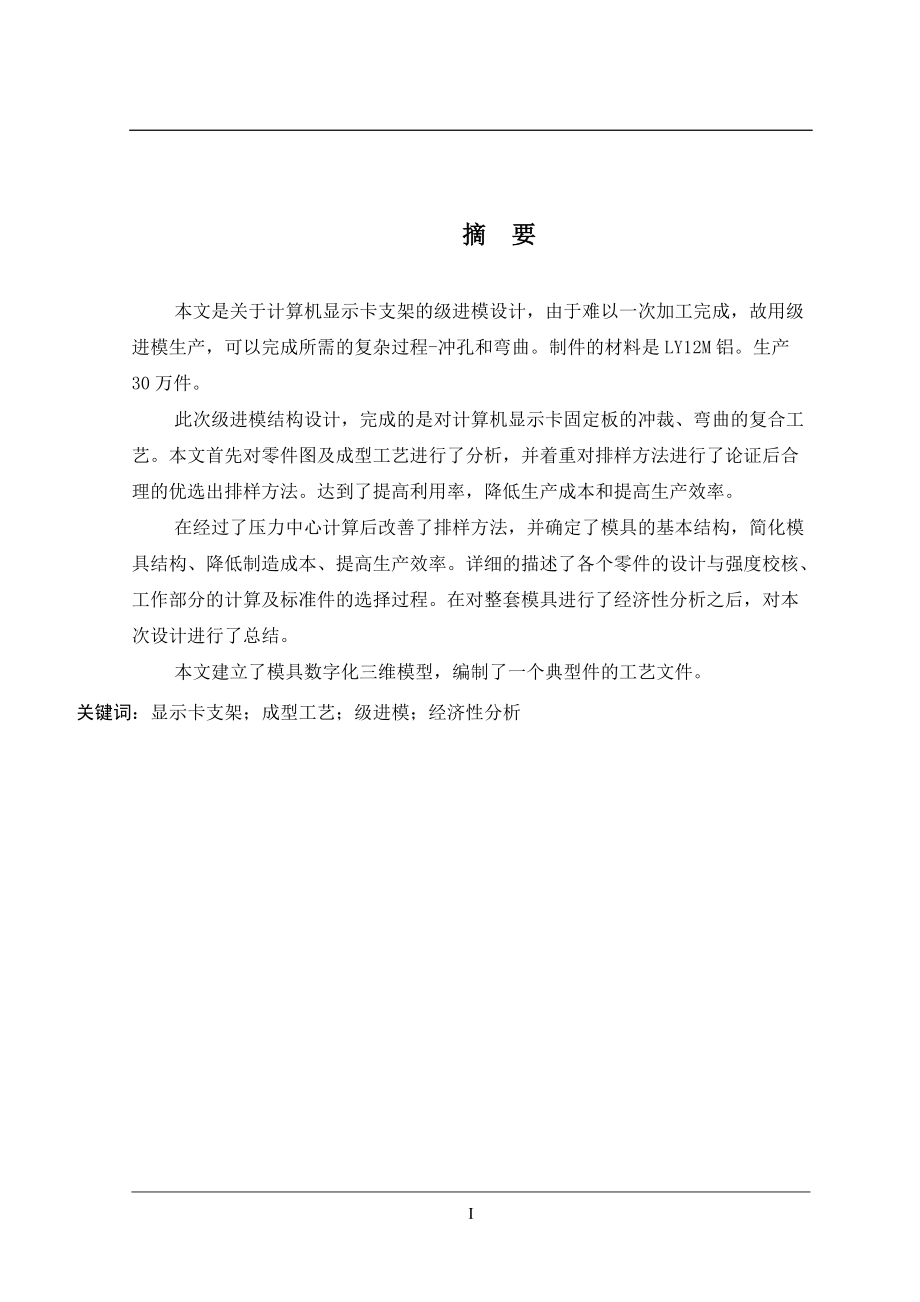


《年產(chǎn)15000噸嬰兒配方粉工廠設(shè)計(jì)模具專業(yè)畢業(yè)論文》由會(huì)員分享,可在線閱讀,更多相關(guān)《年產(chǎn)15000噸嬰兒配方粉工廠設(shè)計(jì)模具專業(yè)畢業(yè)論文(76頁(yè)珍藏版)》請(qǐng)?jiān)谘b配圖網(wǎng)上搜索。
1、 摘 要 本文是關(guān)于計(jì)算機(jī)顯示卡支架的級(jí)進(jìn)模設(shè)計(jì),由于難以一次加工完成,故用級(jí)進(jìn)模生產(chǎn),可以完成所需的復(fù)雜過(guò)程-沖孔和彎曲。制件的材料是LY12M鋁。生產(chǎn)30萬(wàn)件。 此次級(jí)進(jìn)模結(jié)構(gòu)設(shè)計(jì),完成的是對(duì)計(jì)算機(jī)顯示卡固定板的沖裁、彎曲的復(fù)合工藝。本文首先對(duì)零件圖及成型工藝進(jìn)行了分析,并著重對(duì)排樣方法進(jìn)行了論證后合理的優(yōu)選出排樣方法。達(dá)到了提高利用率,降低生產(chǎn)成本和提高生產(chǎn)效率。 在經(jīng)過(guò)了壓力中心計(jì)算后改善了排樣方法,并確定了模具的基本結(jié)構(gòu),簡(jiǎn)化模具結(jié)構(gòu)、降低制造成本、提高生產(chǎn)效率。詳細(xì)的描述了各個(gè)零件的設(shè)計(jì)與強(qiáng)度校核、工作部分的計(jì)算及標(biāo)準(zhǔn)件的選擇過(guò)程。在對(duì)整套模具進(jìn)行了經(jīng)濟(jì)性分析之后,對(duì)本
2、次設(shè)計(jì)進(jìn)行了總結(jié)。 本文建立了模具數(shù)字化三維模型,編制了一個(gè)典型件的工藝文件。 關(guān)鍵詞:顯示卡支架;成型工藝;級(jí)進(jìn)模;經(jīng)濟(jì)性分析 Abstract This desighn is about the Stent of Computer Graphics.It’s hard to process and has difficulty to punch once.The multi-station progressive die assumped in this paper can finish the complex process—blanking and bending. The
3、 material of products is LY12M aluminum.The output is 300,000 Pieces. At this time designed of progressive die complet rushing to cut and curving compound technology of The Stent of Computer Graphics. This paper first analyses for part drawing and Bending technology, after expounding and proving em
4、phatically for queuing up shape method, it is reasonable and good to choose row shape method, the location of the gate and the knockout way, reduces the production costs and increases the production efficiency. . After having passed pressure central calculation, have improved row shape method , an
5、d have determined the basic structure of mould. Described detailed course of selecting of every standard componentthat has been designed and calculation. Summarized after having carried out economy analysis for complete die full paper. It built a 3D model of the die, compiled the process of a typi
6、cal part. Keywords: Computer Graphics; type technology; row shape method; economy analysis 目 錄 1 引言 1 1.1 級(jí)進(jìn)模概述 1 1.2 畢業(yè)設(shè)計(jì)內(nèi)容、步驟 2 2 零件圖及成形工藝性分析 3 2.1 零件圖的尺寸公差及技術(shù)要求 3 2.2 LY12M鋁合金磁盤芯軸的機(jī)械性能 4 2.3 彎曲件的工藝性分析 4 2.3.1 成型分析 4 2.3.2 彎曲件直邊的高度 4 2.3.3 彎曲件孔邊的距離 4 2.3.4 彎曲件的回彈 5 2.4 確定工藝方案 5 3
7、 毛坯尺寸的計(jì)算及方案確定 6 3.1 毛坯展開尺寸的計(jì)算 6 3.2 排樣圖工藝分析 7 3.2.1 橫排工藝分析(方案一) 7 3.2.2 縱排排樣分析(方案二) 8 3.3 優(yōu)選分析 9 3.4 壓力中心的計(jì)算 9 3.5 排樣圖的確定 14 3.5.1 排樣圖設(shè)計(jì)原理 14 3.5.2 載體設(shè)置的確定 14 3.5.3 確定工位數(shù) 14 3.5.4 步距精度和定距方式 15 3.6 沖裁間隙 15 4 模具結(jié)構(gòu)設(shè)計(jì)與強(qiáng)度校核 16 4.1 模架的選擇 16 4.2 凹模的設(shè)計(jì)與校核 16 4.2.1 凹模外形尺寸設(shè)計(jì) 16 4.2.2 凹模與邊緣最小值
8、 17 4.2.3 凹模上螺釘孔,圓柱銷孔的小距離 17 4.2.4 凹模材料 17 4.2.5 凹模強(qiáng)度的校核 17 4.3 導(dǎo)料板的設(shè)計(jì) 18 4.4 凸模的設(shè)計(jì) 18 4.4.1 圓形凸模的設(shè)計(jì)與校核 18 4.4.2 材料選擇 18 4.4.3 凸模強(qiáng)度校核 18 4.4.4 異形凸模(沖裁) 19 4.4.5 彎曲凸模的設(shè)計(jì) 20 4.5 浮頂器的設(shè)計(jì) 20 4.5.1 浮頂器的選用 20 4.5.2 材料選擇 21 4.6 卸料裝置的設(shè)計(jì) 21 4.6.1 卸料板的結(jié)構(gòu)形式 21 4.6.2 材料的選擇 21 4.7 固定板的設(shè)計(jì) 21 4.7.
9、1 厚度的確定 21 4.7.2 結(jié)構(gòu)形式的確定 22 4.8 墊板的設(shè)計(jì)與校核 22 4.8.1 上墊板 22 4.8.2 材料的選擇 22 4.8.3 強(qiáng)度校核 23 4.8.4 下墊板 23 4.9 模柄的選用 23 4.10 彈性元件的選用 24 4.10.1 關(guān)于卸料彈簧力的計(jì)算 24 4.10.2 選擇卸料彈簧 24 4.11 卸料螺釘?shù)倪x擇 25 4.12 導(dǎo)向裝置的確定 26 4.13 各板厚度、模具閉合高度 26 5 模具零件的工作部分計(jì)算 27 5.1 沖裁部分尺寸計(jì)算:(線切割加工) 27 5.1.1 在第二工位沖2個(gè)孔 27 5.1.2
10、 尺寸轉(zhuǎn)換 27 5.1.3 尺寸校核 27 5.1.4 壓力的計(jì)算 28 5.2 第三工位沖一個(gè)孔 28 5.2.1基本尺寸計(jì)算 28 5.2.2 尺寸轉(zhuǎn)換 28 5.2.3 尺寸校核 29 5.2.4 壓力的計(jì)算 29 5.3 第四工位沖中間方孔 29 5.3.1基本尺寸計(jì)算 29 5.3.2 尺寸轉(zhuǎn)換 30 5.3.3 壓力的計(jì)算 31 5.4 第三工位沖下方孔 31 5.4.1基本尺寸計(jì)算 31 5.4.2 尺寸轉(zhuǎn)換 32 5.4.3 壓力的計(jì)算 33 5.5 第四工位切削模1的相關(guān)計(jì)算 33 5.5.1基本尺寸計(jì)算 33 5.5.2 尺寸轉(zhuǎn)換 34
11、 5.5.3 壓力計(jì)算 35 5.6 第五工位側(cè)方孔 35 5.6.1 基本尺寸計(jì)算 35 5.6.2 尺寸轉(zhuǎn)換 35 5.6.3 壓力計(jì)算 37 5.7 彎曲面刃口 38 5.7.1基本尺寸計(jì)算 38 5.7.2 尺寸轉(zhuǎn)換 38 5.7.3 壓力計(jì)算 39 5.8 切削模2刃口的尺寸計(jì)算 40 5.8.1基本尺寸計(jì)算 40 5.8.2 尺寸轉(zhuǎn)換 41 5.8.3 壓力計(jì)算 42 5.9 第七工位彎曲凸凹模圓角半徑及彎曲深度的確定 42 5.10 第八工步落料部分尺寸計(jì)算 43 5.11 側(cè)刃的尺寸計(jì)算 45 6 定位系統(tǒng)的確定 48 6.1 側(cè)刃定位設(shè)計(jì)
12、48 6.2 導(dǎo)正銷設(shè)計(jì) 49 6.2.1導(dǎo)正釘孔直徑的設(shè)計(jì) 49 6.2.2導(dǎo)正釘工作直徑與導(dǎo)正釘孔徑的關(guān)系 49 6.2.4導(dǎo)正釘?shù)陌惭b形式 50 7 壓力機(jī)的選擇 51 7.1 壓力計(jì)算 51 7.2 選用壓力機(jī) 51 8 經(jīng)濟(jì)性分析 53 8.1 主要從以下幾方面考慮價(jià)格 53 8.2 級(jí)進(jìn)模價(jià)格的簡(jiǎn)單估算 53 9 凹模的加工工藝 55 10 三維實(shí)體建模 56 10.1 CATIA的概述 56 10.2 CATIA V5基本功能的簡(jiǎn)介 57 10.2.1 CATIA V5的模塊 57 10.2.2 CATIA V5用戶界面 57 10.3 零件的設(shè)
13、計(jì) 58 10.3.1 圓注銷的確定 58 10.3.2 卸料板的設(shè)計(jì) 59 10.3.3墊板的設(shè)計(jì) 60 10.3.4模柄的設(shè)計(jì) 60 10.4 裝配編輯零件 61 10.4.1 按裝配關(guān)系設(shè)計(jì)新零件 61 10.4.2 自動(dòng)捕捉部件對(duì)齊 63 11 結(jié)論 65 參考文獻(xiàn) 66 致 謝 67 VII 1 引言 多工位級(jí)進(jìn)模的結(jié)構(gòu)比較復(fù)雜,模具設(shè)計(jì)和制造技術(shù)要求較高,同時(shí)對(duì)沖壓設(shè)備、原材料也有相應(yīng)的要求,模具的成本高。因此,在模具設(shè)計(jì)前必須對(duì)工件進(jìn)行全面分析,然后合理確定該工件的沖壓成形工藝方案,正確設(shè)計(jì)模具結(jié)構(gòu)和模具零件的加工工藝規(guī)程,以獲得最佳
14、的技術(shù)經(jīng)濟(jì)效益。顯然,采用多工位級(jí)進(jìn)模進(jìn)行沖壓成形與采用普通沖模進(jìn)行沖壓成形在沖壓成形工藝、模具結(jié)構(gòu)設(shè)計(jì)及模具加工等方面存在許多不同,本章將重點(diǎn)介紹它們?cè)跊_壓工藝與模具設(shè)計(jì)上的不同之處。 1.1 級(jí)進(jìn)模概述 多工位級(jí)進(jìn)模是在普通級(jí)進(jìn)模的基礎(chǔ)上發(fā)展起來(lái)的一種高精度、高效率、長(zhǎng)壽命的模具,是技術(shù)密集型模具的重要代表,是沖模發(fā)展方向之一。這種模具除進(jìn)行沖孔落料工作外,還可根據(jù)零件結(jié)構(gòu)的特點(diǎn)和成形性質(zhì),完成壓筋、沖窩、彎曲、拉深等成形工序,甚至還可以在模具中完成裝配工序。沖壓時(shí),將帶料或條料由模具入口端送進(jìn)后,在嚴(yán)格控制步距精度的條件下,按照成形工藝安排的順序,通過(guò)各工位的連續(xù)沖壓,在最后工位經(jīng)沖
15、裁或切斷后,便可沖制出符合產(chǎn)品要求的沖壓件。為保證多工位級(jí)進(jìn)模的正常工作,模具必須具有高精度的導(dǎo)向和準(zhǔn)確的定距系統(tǒng),配備有自動(dòng)送料、自動(dòng)出件、安全檢測(cè)等裝置。所以多工位級(jí)進(jìn)模與普通沖模相比要復(fù)雜,具有如下特點(diǎn): (1) 在一副模具中,可以完成包括沖裁,彎曲,拉深和成形等多道沖壓工序;減少了使用多副模具的周轉(zhuǎn)和重復(fù)定位過(guò)程,顯著提高了勞動(dòng)生產(chǎn)率和設(shè)備利用率。 (2) 由于在級(jí)進(jìn)模中工序可以分散在不同的工位上,故不存在復(fù)合模的“最小壁厚”問(wèn)題,設(shè)計(jì)時(shí)還可根據(jù)模具強(qiáng)度和模具的裝配需要留出空工位,從而保證模具的強(qiáng)度和裝配空間。 (3) 多工位級(jí)進(jìn)模通常具有高精度的內(nèi)、外導(dǎo)向(除模架導(dǎo)向精度要求高
16、外,還必須對(duì)細(xì)小凸模實(shí)施內(nèi)導(dǎo)向保護(hù))和準(zhǔn)確的定距系統(tǒng),以保證產(chǎn)品零件的加工精度和模具壽命。 (4) 多工位級(jí)進(jìn)模常采用高速?zèng)_床生產(chǎn)沖壓件,模具采用了自動(dòng)送料、自動(dòng)出件、安全檢測(cè)等自動(dòng)化裝置,操作安全,具有較高的生產(chǎn)效率。目前,世界上最先進(jìn)的多工位級(jí)進(jìn)模工位數(shù)多達(dá)50多個(gè),沖壓速度達(dá)1000次/分以上。 (5) 多工位級(jí)進(jìn)模結(jié)構(gòu)復(fù)雜,鑲塊較多,模具制造精度要求很高,給模具的制造、調(diào)試及維修帶來(lái)一定的難度。同時(shí)要求模具零件具有互換性,在模具零件磨損或損壞后要求更換迅速,方便,可靠。所以模具工作零件選材必須好(常采用高強(qiáng)度的高合金工具鋼、高速鋼或硬質(zhì)合金等材料),必須應(yīng)用慢走絲線切割加工、成型
17、磨削、坐標(biāo)鏜、坐標(biāo)磨等先進(jìn)加工方法制造模具。 (6) 多工位級(jí)進(jìn)模主要用于沖制厚度較?。ㄒ话悴怀^(guò)2mm)、產(chǎn)量大,形狀復(fù)雜、精度要求較高的中、小型零件。用這種模具沖制的零件,精度可達(dá)IT10級(jí)。 1.2 畢業(yè)設(shè)計(jì)內(nèi)容、步驟 1.查閱資料、調(diào)研、熟悉畢業(yè)設(shè)計(jì)題目: 2.檢查及繪制制件圖、計(jì)算及繪制展開圖(4#圖紙一張) 3.沖壓件工藝分析,工序設(shè)計(jì)計(jì)算,編制排樣圖(用3#圖紙一張,含沖壓力計(jì)算,初選壓力機(jī)) 4.選擇模具結(jié)構(gòu),結(jié)構(gòu)設(shè)計(jì)、計(jì)算。 5.繪制模具草圖、交審。 6.模具工作尺寸及壓力機(jī)參數(shù)計(jì)算。 7.繪制模具裝配圖。 8.繪制模具零件圖。 9.對(duì)設(shè)計(jì)方案進(jìn)行經(jīng)濟(jì)分
18、析及編寫中等復(fù)雜程度模具零件制造工藝流程一份。 10.編寫畢業(yè)設(shè)計(jì)說(shuō)明書。翻譯外文資料一份。 11.指導(dǎo)教師審閱,批審教師審閱,答辯委員會(huì)審查,學(xué)生答辯 2 零件圖及成形工藝性分析 由于制件是先沖孔后彎曲,彎曲部分較簡(jiǎn)單但沖孔較多且較集中,能在設(shè)計(jì)中做到合理切邊落料且不干涉,,這是模具加工零件中應(yīng)注意的地方。下面對(duì)其具體內(nèi)容進(jìn)行分析及闡述。 2.1 零件圖的尺寸公差及技術(shù)要求 零件的材料是硬鋁LY12M,其料厚為t=1.0mm。 圖2.1是計(jì)算機(jī)顯卡支架零件,需要沖孔、彎曲、落料等工序。首先將件展開觀察零件的形(如圖2.2),零件是一個(gè)外形規(guī)整,彎曲較容易的制件。 圖2
19、.1 零件圖 圖2.2 零件展開圖 2.2 LY12M鋁合金磁盤芯軸的機(jī)械性能 研究材料的金屬性能,以其各項(xiàng)機(jī)械性能數(shù)據(jù)進(jìn)行沖裁、翻邊的模具設(shè)計(jì),能最好的利用材料,避免發(fā)生破裂和變形,達(dá)到設(shè)計(jì)要求,完成設(shè)計(jì)任務(wù)。 LY12M的各項(xiàng)機(jī)械性能如下: 抗剪強(qiáng)度 280MPa 抗拉強(qiáng)度 420MPa 延伸率 25% 屈服強(qiáng)度 368MPa 彈性模量E 72GPa 2.3 彎曲件的工藝性分析 彎曲加工分上下彎曲兩種方式,本設(shè)計(jì)采用的上直接向下彎曲的方式。為保證彎曲的標(biāo)準(zhǔn),以下對(duì)彎曲部分進(jìn)行了分析和介紹。 2.3.1 成型分析 材料是LY
20、12(淬硬并經(jīng)自然時(shí)效),厚度是1.0mm,制件的彎曲內(nèi)半徑是R0.5mm,大于硬鋁允許的最小彎曲半徑,所以可以彎成。 2.3.2 彎曲件直邊的高度 當(dāng)彎曲角時(shí),為了保證工件的彎曲質(zhì)量,必須保證彎曲件的直邊高度為h>2t;若h<2t,則必須先壓槽彎曲或加高直邊,彎曲后再切掉多余的部分.對(duì)于壓制件,彎曲高度=12mm,大于2t=2.0.所以不必加高直邊或壓槽即可彎成 。 2.3.3 彎曲件孔邊的距離 當(dāng)彎曲有孔的毛坯時(shí),如果孔位于彎曲區(qū)附近,則彎曲時(shí)孔的形狀會(huì)發(fā)生變形,為了避免這種情況,必須使孔位于變形區(qū)外,從孔邊到彎曲半徑中心的距離取為當(dāng)t<2mm時(shí),。 t=1.0; 所以s≥0.
21、1mm。如圖2.3 圖2.3 彎曲區(qū)附近孔示意圖 2.3.4 彎曲件的回彈 對(duì)于r/t<5的彎曲件,由于彎曲半徑較小,其彎曲半徑變化較小,因此一般只考慮彎角的回彈量,半徑的變化可忽略。 由于本制件包含了多個(gè) 成形工序,由單一的沖裁或彎曲都完成不了,且造價(jià)比較高,因此,在精度和經(jīng)濟(jì)上,本制件采用了多工位級(jí)進(jìn)摸制造。 2.4 確定工藝方案 根據(jù)零件的形狀和材料的機(jī)械性能,安排擬訂沖壓工藝方案,達(dá)到最經(jīng)濟(jì)合理的工藝方案。 基本工序:沖裁、彎曲。可擬定如下兩種工藝方案 方案一:用簡(jiǎn)單模分次加工,即沖孔,落料,彎曲。 方案二:用級(jí)進(jìn)模沖制 采用方案一,生產(chǎn)率低,工件尺寸的累積誤差
22、大,操作不方便,不安全,由于該零件屬于大批量生產(chǎn),能夠用沖壓加工,現(xiàn)選用方案二。 3 毛坯尺寸的計(jì)算及方案確定 中值法求展開長(zhǎng)度。取彎曲件各尺寸的中限值作為尺寸鏈計(jì)算的依據(jù),求出展開長(zhǎng)度的中限值,把沖件有關(guān)尺寸公差提高3到4個(gè)等級(jí)的公差作為展開長(zhǎng)度公差,其偏差為對(duì)稱分布。計(jì)算模具尺寸時(shí)候,也以沖件的中限值作為計(jì)算依據(jù),模具公差取IT7到IT8級(jí),其偏差也對(duì)稱分布。 3.1 毛坯展開尺寸的計(jì)算 已知沖件如圖3.1求彎曲件展開長(zhǎng)度 圖3.1 零件側(cè)視圖 零件彎曲部分展開尺寸的計(jì)算 L=L1+L2+L3=12+2.4+119=133.4(mm) 其中L為增環(huán),L2,L3為
23、減環(huán) 所以 L1max=Lmax-L2min-L3min=12.24mm L1min=Lmin-L2max-L3max=11.76mm Lmax=L1max+L2min+L3min=133.48mm Lmin=L1min+L2max+L3max=133.32mm 確定各段極值: Lmax=133.48mm, Lmin=133.32mm.最后確定L=133.4mm. 公差等級(jí)為IT14級(jí),提高4個(gè)等級(jí)為IT10級(jí),等級(jí)公差為0.040,所以展開長(zhǎng)度為133.4mm0.02。 3.2 排樣圖工藝分析 排樣的設(shè)計(jì)直接關(guān)系到生產(chǎn)的效率、經(jīng)濟(jì)性、合理性和可行性。所以設(shè)計(jì)科學(xué)的排樣方式是設(shè)
24、計(jì)級(jí)進(jìn)模的前提首要工作。 3.2.1 橫排工藝分析(方案一) 1) 材料利用率: 當(dāng)采用橫排時(shí), 這樣,毛坯的寬度B=。 b=B+2a=133.4+21.5=136.4mm 料寬為133.4mm 條料的步距P=B+a=133.4+1.5=134.9mm l=L+a+a1=18+1.5+1.8=21.3mm 利用率=(aB)/(a1L) 100%=74% 2) 出料:采用下出料,在最后一個(gè)工步切邊落零件,(在凹模設(shè)置斜面)零件 滑后,在下出料部位設(shè)置抽屜收集零件。 3) 廢料清除:廢料皆是下出料,露到下模設(shè)計(jì)的抽屜中有工人清除。 4) 導(dǎo)正:首先在第一個(gè)工步中沖出
25、直徑為5mm工藝空用來(lái)精定位。粗定位由側(cè) 刃裝置保證。在最后一個(gè)落料工步中沖出零件所要求的Φ7的孔。 5) 抬料:由于彎曲工步后便是落料切邊,因此可以設(shè)置躲避槽,抬料高度降低 至3mm,使用浮頂器即可。 備注:上述排樣模具制造簡(jiǎn)單,但材料利用率比較低。 3.2.2 縱排排樣分析(方案二) 圖3.2 縱排排樣圖 (1)材料利用率: 當(dāng)采用縱排時(shí),這樣,毛坯的寬度B=18mm。 由零件圖可以看出,零件的寬度為18,根據(jù)最大的尺寸確定條料的步距P。 所以,條料的步距P= 18+1.5=19.5。 b=l+2a=
26、21.3+21.5=24.3mm l=B+a+a1=18+1.5+1.8=21.3mm 利用率=(aB)/(a1L) 100%=97% (2)出料:采用下出料,在最后一個(gè)工步切邊(在凹模設(shè)置斜面),同時(shí)設(shè)計(jì)頂件機(jī)構(gòu)頂出另外一個(gè)零件,在下出料部位設(shè)置抽屜收集零件。 (3)廢料清除:廢料皆是下出料,露到下模設(shè)計(jì)的抽屜中有工人清除。 (4)導(dǎo)正:首先在第一個(gè)工步中沖出直徑為5mm工藝空用來(lái)精定位。粗定位由側(cè)刃裝置保證。在最后一個(gè)落料工步中沖出零件所要求的Φ7的孔。 (5)抬料:由于彎曲工步后便是落料切邊,因此可以設(shè)置躲避槽,抬料高度降低至3mm,使用浮頂器即可。 (6)備注:上述排樣模
27、具制造簡(jiǎn)單,且材料利用率比較高。 零件的寬度為18,條料的步距P=19.8mm 3.3 優(yōu)選分析 兩種派樣法,首選排樣2即縱排,材料利用率高,已經(jīng)達(dá)到了90%以上。工件的精度在出件時(shí)候可以得到保證,而且工件出件容易,模具的維護(hù)也相對(duì)容易,出件順利,體現(xiàn)了級(jí)進(jìn)模高度自動(dòng)化的優(yōu)點(diǎn)。另一重種排樣方法,模具設(shè)計(jì)制造和維護(hù)基本相同,但利用率不高。由于后種采用橫排的方式排樣,在最后出料時(shí)候要設(shè)計(jì)頂件的裝置,在模具持續(xù)工作時(shí)候難以使零件順利出件且不影響自動(dòng)送料裝置的繼續(xù)送料。雖然對(duì)排可以使材料利用率達(dá)到80%以上,但考慮到模具的設(shè)計(jì)一切為了最后得到零件,所以采用第二種排樣方法是優(yōu)選。 3.4 壓力中
28、心的計(jì)算 圖3.6 排樣圖 排樣圖分8步: (1)沖側(cè)刃 (2)沖定位孔(亦顯卡固定螺栓用孔) ---落料沖孔 (3)沖上圓和下方孔---沖孔 (4)沖側(cè)兩中間方孔及下方切費(fèi)料---沖孔 (5)沖彎曲邊上孔及下方側(cè)孔---沖孔 (6)切上方廢料---落料 (7)彎曲---彎曲 (8)切斷---落料 選取圖3.7所示的坐標(biāo)系: 圖3.7 凸模的排列 由凸模排樣圖,可以看出在板料上,孔和加工落料部分都是不對(duì)稱和不規(guī)則的,不規(guī)則的孔為側(cè)刃孔和2個(gè)廢料切口,分別計(jì)算這3個(gè)孔的壓力中心。 1、廢料切模1的沖壓中心: 圖3.8切口模的坐標(biāo)值 沖模的壓力中心到坐
29、標(biāo)軸的距離按下式確定: 到y(tǒng)軸的距離: (3-1) 到x軸的距離: (3-2) 其中:L1、L2、L3、L4、L5、L6—各凸模工作部分剖面輪廓的周長(zhǎng)。 ∴廢料切模的壓力中心為: x=52.48 y= 65.9 2.廢料切模1的沖壓中心: 圖3.9 切口模的坐標(biāo)值 沖模的壓力中心到坐標(biāo)軸的距離按下式確定: 到x軸的距離: 根據(jù)式(3-2),得 y=(
30、L1y1+L2y2+L3y3+L4y4+L5y5+L6y6)/( L1+L2+L3+L4+L5+L6) 到y(tǒng)軸的距離: 根據(jù)式(3-1),得 x=(L1x1+L2x2+L3x3+L4x4+L5x5+L6x6)/( L1+L2+L3+L4+L5+L6) 其中:L1、L2、L3、L4、L5、L6—各凸模工作部分剖面輪廓的周長(zhǎng)。 ∴廢料切模的壓力中心為: x= 99.2 y= -69.5 3、側(cè)刃的沖壓中心: 圖3.10 側(cè)刃的坐標(biāo)值 根據(jù)式(3-1)、(3-2可以計(jì)算得到,側(cè)刃的壓力中心x、y: x=152 (x
31、=152) y=68.4 (y=-68.4) 最后綜合各部分的壓力中心, 根據(jù)公式確定排樣的壓力中心: 最后確定 壓力中心坐標(biāo)為X=64,Y=23.6 3.5 排樣圖的確定 3.5.1 排樣圖設(shè)計(jì)原理 導(dǎo)正釘孔位置的安置對(duì)于多工位級(jí)進(jìn)模的精確定位是很關(guān)鍵的。必須在材料排樣圖的第一工位沖出工藝性導(dǎo)正釘孔,在第二工位以后每隔一個(gè)工位相應(yīng)的設(shè)置導(dǎo)正釘孔。導(dǎo)正釘孔徑應(yīng)大于或等于四倍的料厚。故本模具導(dǎo)正釘孔徑需4.0mm,考慮到材料的最小搭邊值及零件本身中間方孔兩側(cè)的直徑3mm的孔,設(shè)計(jì)導(dǎo)正釘孔徑3mm,并安排在第一工位沖出。為了提高定位精度采用三種定位方式聯(lián)合使用,即側(cè)刃與導(dǎo)正銷
32、和擋塊聯(lián)合使用。 凹模型孔之間的最小間隙應(yīng)適當(dāng),級(jí)進(jìn)模適合沖壓薄料,一般料厚為0.1~1.2mm,最后的達(dá)到2.0mm,在這種情況下對(duì)于圓形孔間隔可取2.5t最小不小于2mm,對(duì)異形孔其間隔應(yīng)當(dāng)適當(dāng)放大些??朔慰妆∪醐h(huán)節(jié)避免形孔有尖角、狹槽、細(xì)腰等薄弱環(huán)節(jié),保證凸凹模的強(qiáng)度,也便于凸凹模的制造。 盡量減少空步,空步的設(shè)置,不僅增加了相關(guān)工步之間的距離,加大了制造與沖壓的誤差,增大了模具的面積。所以只有當(dāng)相鄰工步之間空間距離過(guò)小的時(shí)候,難以保證凸凹模強(qiáng)度或難以設(shè)置必要機(jī)構(gòu)時(shí)才可以設(shè)置空步。 3.5.2 載體設(shè)置的確定 零件有一個(gè)彎曲直角,寬度為15mm。因?yàn)榱慵情L(zhǎng)條形,表面平整,L形
33、彎曲,設(shè)計(jì)載體寬度為16mm,高度為40。其具體尺寸看零件圖。裝配時(shí)以H7/k6配合。 3.5.3 確定工位數(shù) 第一工位先側(cè)刃切邊,第二工步?jīng)_導(dǎo)正釘孔。導(dǎo)正釘孔是必須先沖的孔。第二、三、四、五、六工位對(duì)零件進(jìn)行導(dǎo)正、沖切外形,第七步是對(duì)已經(jīng)沖切好外形的零件進(jìn)行向下彎曲,第八工位落料,設(shè)置斜坡落零件。故整個(gè)成形過(guò)程分為八個(gè)工位。 3.5.4 步距精度和定距方式 步距精度 影響步距精度的因素很多,歸納起來(lái)主要有:沖件的精度的等級(jí)、形狀復(fù)雜程度、沖件材質(zhì)和厚度,模具的工位數(shù);沖制時(shí)條料的送進(jìn)方式和定距形式等。據(jù)實(shí)踐得經(jīng)驗(yàn)公式: 式
34、中:——多工位級(jí)進(jìn)模步距對(duì)稱偏差差值; ——沖件沿件條料送進(jìn)方向最大輪廓基本尺寸(展開后)精度提高三級(jí)后的實(shí)際公差值。 n——模具設(shè)計(jì)的工位數(shù); k——修正系數(shù)。 定距方式 模具結(jié)構(gòu)采用雙側(cè)刃定距:即在條料的雙側(cè)沖去多余邊料,并用側(cè)刃檔塊進(jìn)行初定位,用定位釘進(jìn)行精定位。 排樣方案合格。 3.6 沖裁間隙 C——單面沖裁間隙; K——沖裁系數(shù),對(duì)于一般沖裁件,k=3時(shí)可獲得較小的沖裁毛刺、沖裁力和最高的模具壽命; ——材料的抗剪強(qiáng)度(MPa); t——材料厚度(mm); 4 模具結(jié)構(gòu)設(shè)計(jì)與強(qiáng)度校核 4.1 模架的選
35、擇 由于本模具較大,故根據(jù)凹模邊界選用標(biāo)準(zhǔn)四導(dǎo)柱的上下模座,規(guī)格如下: 凹模邊界 400250 上模座 40025050 技術(shù)條件按JB/T8070——1995的規(guī)定 下模座 40025060 技術(shù)條件按JB/T8070——1995的規(guī)定 導(dǎo)柱 40230/45230 GB/T2861.1 導(dǎo)套 4012548/4512548 GB/T2861.6 4.2 凹模的設(shè)計(jì)與校核 對(duì)于多工位級(jí)進(jìn)模,不論其凹模的形孔多少,復(fù)雜程度如何,凹模設(shè)計(jì)成一個(gè)整體的稱為整體凹模。但對(duì)于多工位級(jí)進(jìn)模來(lái)說(shuō)缺點(diǎn)較多:(1)凹模形
36、孔孔距只有靠機(jī)床的坐標(biāo)精度和工人的技術(shù)水平來(lái)保證。(2)可能由于形孔局部制造誤差導(dǎo)致整個(gè)凹模板的報(bào)廢。也可能由于凹模局部的損壞,而造成整個(gè)凹模板的報(bào)廢。但是一塊凹模對(duì)于安裝來(lái)說(shuō)就較簡(jiǎn)單,且堅(jiān)固性較好,定位也較容易,因此本凹模仍采用整體式在部分工位設(shè)置鑲塊,用螺釘和銷釘將凹模固定在下模座上。選擇M10的螺栓共選取8個(gè),兩個(gè)銷釘用mm的。凹模形孔、螺釘、銷釘布置見零件圖。 4.2.1 凹模外形尺寸設(shè)計(jì) 凹模的外形尺寸設(shè)計(jì)的依據(jù)是根據(jù)各凹模的相應(yīng)位置分布、定位件和固定件最小邊距等的配合尺寸綜合考慮得出的設(shè)計(jì)依據(jù)。本設(shè)計(jì)中,根據(jù)設(shè)計(jì)需要的實(shí)際情況和經(jīng)濟(jì)性,按照標(biāo)準(zhǔn)件數(shù)據(jù)尺寸,合理地采用了如下的尺寸
37、數(shù)據(jù): 凹模長(zhǎng)L=400,寬B=250,高H=40. 凹模最小高度按經(jīng)驗(yàn)公式計(jì)算 h=kb(h≥15mm) 系數(shù)k查表得0.22; b為最大孔尺寸108mm. h=0.22108=23.76 mm 故設(shè)計(jì)合理,高度達(dá)到要求。 4.2.2 凹模與邊緣最小值 查表(沖壓手冊(cè)表2-41)得33mm,刃口與刃口間不應(yīng)小于5mm。 4.2.3 凹模上螺釘孔,圓柱銷孔的小距離 查表得:M10淬火后A≥14 B≥17 C≥5 D≥8 圖4.1 邊孔距離示意圖 4.2.4 凹模材料 凹模材料的選擇要能夠滿足各種沖裁、彎曲、落料的強(qiáng)度要求和剛度要
38、求,還要考慮到模具的經(jīng)濟(jì)性,適宜生產(chǎn)和制造。 由于沖裁形狀復(fù)雜,批量大,,故選用T10A,HRC60~62。 4.2.5 凹模強(qiáng)度的校核 由于工作時(shí)受彎曲力,如果凹模高度不夠便會(huì)產(chǎn)生彎曲變形,以致于損壞。 F——沖裁力,——許用彎曲應(yīng)力,為MPa(淬火剛為未淬火剛的1.5~3倍)?!寄W钚『穸?,單位mm 故強(qiáng)度夠用。 4.3 導(dǎo)料板的設(shè)計(jì) 由于采用手工送料,可選用不帶臺(tái)階式的導(dǎo)料板,因?yàn)榍懊婵紤]制件向下彎曲后直接滑出凹模,完成零件后零件一部分在模具工作型面下,由于設(shè)有躲避槽,故浮頂器只需抬高零件3mm。導(dǎo)料板取。條料與導(dǎo)料板之間的間隙c=0.05
39、~0.02mm,因?yàn)閷?dǎo)料板是兩塊,所以此間距離及間隔靠裝模時(shí)用定位銷保證。 4.4 凸模的設(shè)計(jì) 4.4.1 圓形凸模的設(shè)計(jì)與校核 沖件的尺寸為3、8均不大,為了加強(qiáng)凸模強(qiáng)度,凸模非工作部分的直徑做成直徑較大的形式,刃口部分尺寸已經(jīng)確定其余尺寸見零件圖,固定方式采用配合,這種形式穩(wěn)定可靠。 4.4.2 材料選擇 凸模的材料選擇要能夠滿足各種凸模固定所需的剛度和強(qiáng)度,還有考慮到經(jīng)濟(jì)性能和制造生產(chǎn)的適宜性。 沖裁形狀簡(jiǎn)單,但生產(chǎn)批量大,所以選擇45,淬硬HRC40~45。 4.4.3 凸模強(qiáng)度校核 (1)凸模的長(zhǎng)度確定,屈服應(yīng)力校核: L= 式中 ——固定板高度mm
40、 ——卸料板高度mm ——墊板的高度mm ——工作行程,取3t=3.6mm h ——附加高度,它包括凸模的修模量,凸模固定板與卸料斑墊板的安全高度。一般取h=15~20mm 。 故L=40+15+20=75mm 對(duì)于圓形凸模,由于凸模直徑較小,容易損壞,故采凸模用了快換結(jié)構(gòu),所以模具長(zhǎng)度為 75+5=80mm 對(duì)于凸模因?yàn)橹挥泄ぷ鞑糠质?,而以上部分做成臺(tái)階,將部分取15mm, 故也符合 要求。 , ——凸模最小直徑mm; t ——料厚; t=1.2mm ——抗剪強(qiáng)度;=441MPa F——
41、沖裁力;=1600MPa 壓應(yīng)力符合要求。 4.4.4 異形凸模(沖裁) 1、異形凸模均采用直通式,其工作形狀與安裝部分形狀基本相同,這樣的異形凸模工藝性好加工精度高,裝卸方便,與固定板采取H7/m6配合,大面積異形凸模采用銷釘固定在凸模固定板上。具體結(jié)構(gòu)見裝配圖及零件圖。 2、材料 因?yàn)闆_裁形狀較復(fù)雜,生產(chǎn)量較大,所以采用;淬硬HRC58~62。 4.4.5 彎曲凸模的設(shè)計(jì) 第七工位有彎曲成形,現(xiàn)在對(duì)其進(jìn)行單獨(dú)的分析設(shè)計(jì)。 由于工位彎曲方向直接向下彎曲。安裝時(shí)卸料板與彎曲凸模間采用H7/n6過(guò)度配合,彎曲上模深入下模內(nèi)直邊高度h=12mm,配合
42、具體結(jié)構(gòu)見裝配圖。由于彎曲力較小,向下L型彎曲采用向下沖彎,因?yàn)閺澢螤詈?jiǎn)單,彎曲力不大,凸模材料選用T8A,淬硬HRC50~55。 由于向下L彎曲長(zhǎng)度較大,將件完全抬起,要抬起大于15mm的高度,因而在凹模上開一個(gè)躲避槽,具體尺寸和結(jié)構(gòu)見裝配圖。由于彎曲力較小而凸模又相對(duì)較大,所以不必校核。 在第八工位,載體沒(méi)有切斷設(shè)置了切斷凸模,將載體切斷。材料:T8A淬硬HRC55~60。 4.5 浮頂器的設(shè)計(jì) 4.5.1 浮頂器的選用 普通型浮頂器,平面端面,且表面要達(dá)到的粗糙度。普通型浮頂器設(shè)置在每個(gè)工步的中心位置。它除了托頂條料浮頂凹模外,不再負(fù)責(zé)其他任務(wù)。它與凹模沒(méi)有嚴(yán)格的配合要求,見
43、圖4.2。結(jié)構(gòu)與分配位置見裝配圖,具體尺寸見零件圖。保證浮頂條料3mm高度。 圖4.2 浮頂器 4.5.2 材料選擇 設(shè)計(jì)和選擇浮頂器,依照設(shè)計(jì)要求的尺寸選擇標(biāo)準(zhǔn)件尺寸的數(shù)據(jù)。按照工藝加工的數(shù)據(jù)考慮頂件力選擇材料。以最經(jīng)濟(jì)和最合理的材料達(dá)到設(shè)計(jì)要求。 考慮到本設(shè)計(jì)中的各項(xiàng)要求和數(shù)據(jù),選擇鋼,淬火硬度HRC40~45。 4.6 卸料裝置的設(shè)計(jì) 4.6.1 卸料板的結(jié)構(gòu)形式 選用彈壓式反凸臺(tái)卸料板,它通過(guò)卸料螺釘、彈簧安裝在模具上,凸臺(tái)部分再下行時(shí)進(jìn)入兩導(dǎo)料板之間,凸臺(tái)與導(dǎo)料板之間有適當(dāng)?shù)拈g隙。卸料板各工作形孔
44、與凹模同心考慮把把卸料板分成兩塊,但由于卸料板的工作較重要,而且兩塊卸料板之間要嚴(yán)格固定,較為困難,故放棄兩塊卸料板的考慮。由于卸料板的卸料力較大,故必須加上輔助導(dǎo)向裝置即小導(dǎo)柱,導(dǎo)套。導(dǎo)套與卸料板之間采用H7/h6過(guò)度配合,卸料板與各凸模配合均為間隙配合,因此各工作形孔要有良好的光潔度。 具體結(jié)構(gòu)及尺寸見零件圖。 4.6.2 材料的選擇 多工位級(jí)進(jìn)模的卸料板應(yīng)具有較好的耐磨性能,并且要有必要的強(qiáng)度,以防止再長(zhǎng)久的受力狀態(tài)下產(chǎn)生變形,所以材料選用鋼,進(jìn)行淬火處理,得到硬度HRC45~50。 4.7 固定板的設(shè)計(jì) 4.7.1 厚度的確定 固定板要裝多數(shù)的凸模,全部的導(dǎo)
45、正釘、小導(dǎo)柱等,并使它們正常穩(wěn)定的工作,要求固定板有足夠的強(qiáng)度和剛性。一般厚度應(yīng)大于最大凸模直徑的2/3,所以H=40mm。 圖4.3 固定板 4.7.2 結(jié)構(gòu)形式的確定 選用整體式,整個(gè)固定板做成一塊,這種形式的凸模固定板的優(yōu)點(diǎn)是制造簡(jiǎn)單,容易達(dá)到精度要求,但在使用中調(diào)整不便。 4.7.3 材料選擇 固定板要有良好的耐磨性和強(qiáng)度,選用鋼淬火硬度HRC45~50。 4.8 墊板的設(shè)計(jì)與校核 4.8.1 上墊板 安裝上墊板的目的是為了防止凸模在沖壓過(guò)程中,由于沖壓力集中而把模座的接觸面壓壞,所以固定半與上模座之間設(shè)置墊板,厚度有時(shí)要考慮彈簧高度,要求墊板加高,所以這里暫時(shí)定
46、為10mm,若以后不夠可加厚 4.8.2 材料的選擇 上墊板位于上模座和凸模固定板之間,起保證模座的接觸面不被沖壓力壓壞的作用,所以其材料的選擇至關(guān)重要,要考慮到材料的機(jī)械性能是否滿足設(shè)計(jì)的要求和經(jīng)濟(jì)性及制造工藝等。 上下墊板采用鋼淬火硬度HRC 43~48 4.8.3 強(qiáng)度校核 選用最大直徑?jīng)_裁凸模進(jìn)行校核 式中:F——沖裁力,N A——承壓面積 ——許用壓力MPa 故強(qiáng)度足夠用。 4.8.4 下墊板 由于下墊板結(jié)構(gòu)和功能基本相似,所以與上選用一樣規(guī)格的即可 4.9 模柄的選用 由于模具比較大,選用壓入式模柄,用一個(gè)止動(dòng)銷
47、防止其轉(zhuǎn)動(dòng),承載能力大,且緊固穩(wěn)定。模柄如圖4.3所示。 圖4.3 模柄 1——模柄 2——上模座 3——止轉(zhuǎn)銷 4.10 彈性元件的選用 在模具中,使用彈性元件提供卸料所需力。因此卸料元件的選擇關(guān)系重大,要能夠滿足卸料力的要求還有符合實(shí)際的尺寸要求及使用。 本設(shè)計(jì)采用的是卸料彈簧,根據(jù)卸料力的大小和模具的設(shè)計(jì)尺寸,按照標(biāo)準(zhǔn)件數(shù)據(jù),選取適宜尺寸。 4.10.1 關(guān)于卸料彈簧力的計(jì)算 卸料彈簧所承受的力 =K 查表得:K=0.04 =212.65 KN 則:
48、=8.5KN 4.10.2 選擇卸料彈簧 卸料力為8520N ,初步設(shè)定采用4個(gè)彈簧,則每個(gè)彈簧所承受的預(yù)壓2630N, 查圓柱螺旋壓縮彈簧表初選彈簧系數(shù): ---------彈簧中徑,=35mm; d----------材料直徑,d=8mm; t-----------節(jié)距,t=11.1mm; n-----------有效圈數(shù),n=4.5; L-----------展開長(zhǎng)度,L=825mm; ---------自由長(zhǎng)度,=65mm; ----------工作極限載荷,=2630N; ----------工作極限負(fù)荷下的變性量,=20.7; 檢查彈簧最大壓縮量是否滿足
49、上述條件: --------彈簧預(yù)壓縮量; --------卸料板工作行程,=t+1=2.2mm; --------凸凹模修磨量,取4mm; ++=11.7+2.2+4=17.9〉11.7 故所選彈簧合適。 查表可知,可選用1090的卸料螺釘(GB2867.6—81)。 彈簧壓縮后長(zhǎng)度為H=65-11.7-2.2=55mm。 4.11 卸料螺釘?shù)倪x擇 選用M10的螺釘。 圖4.4 卸料螺釘及卸料彈簧 長(zhǎng)度L=10+90=100 mm 4.12 導(dǎo)向裝置的確定 導(dǎo)向裝置的選擇 為使卸料板對(duì)凸模起導(dǎo)向作用,根據(jù)沖裁間隙,卸料板與凸模間隙為
50、0.03~0.05(雙面),則小導(dǎo)柱與小導(dǎo)套可以取H7/h6配合。 小導(dǎo)柱,小導(dǎo)套的結(jié)構(gòu)形式如圖5.1。 圖5.1 小導(dǎo)柱 本設(shè)計(jì)選用A型小導(dǎo)柱(GB2861.4-81) d (h6) D (m6) D1 總長(zhǎng)L 18 18 22 65 小導(dǎo)套與卸料板為過(guò)渡配合H7/n6。 4.13 各板厚度、模具閉合高度 上模座50mm 上墊板10mm 固定板40mm 卸料板20mm 凹模40mm 下墊板10mm 下模座60mm 固定板與卸料墊板之間的安
51、全高度取15mm 故模具的合模高度為:245mm 5 模具零件的工作部分計(jì)算 5.1 沖裁部分尺寸計(jì)算:(線切割加工) 根據(jù)單面間隙的計(jì)算公式,得: 5.1.1 在第二工位沖2個(gè)孔 沖孔形面在凸模上,按IT14級(jí)計(jì)算 由公式 得 [1] 5.1.2 尺寸轉(zhuǎn)換 由公式 得 凸模尺寸 * *尺寸按凹模修配,單面間隙0.158~0.182。 5.1.3 尺寸校核 若凸模按0.18配制,則凸模尺寸為 : 3.4
52、0+0.01-0.36=3.05mm 3.40-0.01-0.36=3.03mm 凸模尺寸范圍為3.03~3.05mm之間,均符合尺寸孔的要求。 5.1.4 壓力的計(jì)算 沖孔時(shí)的沖裁力計(jì)算公式為: F2=1.25πτdt (5.1) 其中:d—沖孔件的尺寸。 F2=1.25π3.02801=3297N 因?yàn)樯舷聜€(gè)一個(gè)導(dǎo)正釘孔,所以沖裁力要乘以2.此處的導(dǎo)正釘孔亦是顯卡和支架固定連接的一個(gè)部分. ∴沖導(dǎo)正銷孔時(shí)的沖裁力F=2F2=6594N 5.2 第三工位沖一個(gè)孔 5.2.1基本
53、尺寸計(jì)算 圖5.1 中間圓孔 由公式 得 5.2.2 尺寸轉(zhuǎn)換 由公式 得轉(zhuǎn)化后的凹模尺寸: D=8.25-0.012, 凸模的尺寸可按凹模的尺寸配單面間隙0.03~0.05 *尺寸按凹模修配,單面間隙0.158~0.182。 5.2.3 尺寸校核 若凸模按0.18配制,則凸模尺寸為 3.95+0.01-0.36=3.6mm 3.95-0.01-0.36=3.4mm 孔尺寸范圍為3.4~3.6mm之間,均符合尺寸孔的要求。 5.2.4 壓力的計(jì)算 沖孔時(shí)的沖
54、裁力計(jì)算公式為: F2=1.25πτdt (5.1) 其中:d—沖孔件的尺寸。 F2=1.25π8.02801=8792N 5.3 第四工位沖中間方孔 5.3.1基本尺寸計(jì)算 零件的沖孔尺寸為167, 圖5.2 中方孔 在IT14精度等級(jí)下的標(biāo)準(zhǔn)尺寸為16-0.437-0.3,落料的基準(zhǔn)在凹模上,所以凹模的型面工作尺寸由公式為: 凸模尺寸:Lp=(L+XΔ)+δ ,確定尺寸為:16.225, 7.225 5.3.2 尺寸轉(zhuǎn)換 由公式 凹模尺寸: Ld=(Lp -δ+2C)+δ,確定尺寸為: 16.336+0.04
55、7.336+0.04 (5.2) 凸模尺寸:*16.336、*7.336 其中: Ld、Lp—為凹模、凸模的刃口尺寸。 L—落料件外形的最大極限尺寸。 Δ—沖件的制造公差。 X—磨損系數(shù)。在0.5~1之間取值,他的取值與沖裁精度有關(guān),可查表2-30取值或按下列關(guān)系取值: 當(dāng)沖件的精度在IT10以上時(shí),x=1; 當(dāng)沖件的精度在IT11~I(xiàn)T14時(shí),x=0.75; 當(dāng)沖件的精度在IT14一下時(shí),x=0.5。 零件的沖壓精度IT14,取x=0.75進(jìn)行計(jì)算。 δ—模具的制造公差,分別按照IT6和IT7精度等級(jí)確定凸模和凹模的制造公差。 根據(jù)IT7下可查得凹模的制造偏差分別為:
56、+0.021,+0.018 IT6下可查得凸模的制造偏差分別為:-0.013,-0.011 沖裁間隙C‘的計(jì)算: C’=(ktτ10-4)+0.02t。 計(jì)算得到?jīng)_裁間隙C‘=0.053~0.065。 校核凹模的制造間隙: 在沖裁中模具的制造間隙必須滿足下列的條件: δ凹+δ凸≤2(Cmax-Cmin) 若δ凹+δ凸﹥2(Cmax-Cmin)時(shí), 取δ凹=0.62(Cmax-Cmin),δ凸=0.42(Cmax-Cmin) (5.3) ∴0.021+0.013=0.034>2(0.065-0.053)=0.024, 0.018+0.011=0.029>2(0.0
57、65-0.053)=0.024 這時(shí),取δ凹=0.62(Cmax-Cmin)=0.60.024=0.014,δ凸=0.42(Cmax-Cmin)=0.010。 計(jì)算得到的沖裁間隙過(guò)大,不能保證零件的無(wú)毛刺要求,因此可查表2-26得到H62的沖裁間隙值C=0.03~0.05。 ∴凹模的刃口尺寸為:16.336+0.0147.336+0.010。 5.3.3 壓力的計(jì)算 沖裁力的計(jì)算: 周長(zhǎng)L=16+7+7+16=46。 ∴沖裁F=1.25Ltτ=16100N。 5.4 第三工位沖下方孔 5.4.1基本尺寸計(jì)算 圖5.3 下方孔 由公式 得 凸模尺寸
58、: Lp=(L+XΔ)+δ ,確定尺寸為:18.225, 5.225 5.4.2 尺寸轉(zhuǎn)換 由公式 凹模尺寸: Ld=(Lp -δ+2C)+δ,確定尺寸為: 18.336+0.045.336+0.04 (5.2) 凸模尺寸:*18.336、*5.336 其中: Ld、Lp—為凹模、凸模的刃口尺寸。 L—落料件外形的最大極限尺寸。 Δ—沖件的制造公差。 X—磨損系數(shù)。在0.5~1之間取值,他的取值與沖裁精度有關(guān),可查表2-30取值或按下列關(guān)系取值: 當(dāng)沖件的精度在IT10以上時(shí),x=1; 當(dāng)沖件的精度在IT11~I(xiàn)T14時(shí),x=0.75; 當(dāng)沖件的精度在IT14
59、一下時(shí),x=0.5。 零件的沖壓精度IT14,取x=0.75進(jìn)行計(jì)算。 δ—模具的制造公差,分別按照IT6和IT7精度等級(jí)確定凸模和凹模的制造公差。 根據(jù)IT7下可查得凹模的制造偏差分別為:+0.021,+0.018 IT6下可查得凸模的制造偏差分別為:-0.013,-0.011 沖裁間隙C‘的計(jì)算: C’=(ktτ10-4)+0.02t。[1] 計(jì)算得到?jīng)_裁間隙C‘=0.053~0.065。 校核凹模的制造間隙: 在沖裁中模具的制造間隙必須滿足下列的條件: δ凹+δ凸≤2(Cmax-Cmin) 若δ凹+δ凸﹥2(Cmax-Cmin)時(shí), 取δ凹=0.62(Cmax-
60、Cmin),δ凸=0.42(Cmax-Cmin) (5.3) ∴0.021+0.013=0.034>2(0.065-0.053)=0.024, 0.018+0.011=0.029>2(0.065-0.053)=0.024 這時(shí),取δ凹=0.62(Cmax-Cmin)=0.60.024=0.014, δ凸=0.42(Cmax-Cmin)=0.010。 計(jì)算得到的沖裁間隙過(guò)大,不能保證零件的無(wú)毛刺要求,因此可查表2-26得到H62的沖裁間隙值C=0.03~0.05。 ∴凹模的刃口尺寸為:18.336+0.0145.336+0.010。 凸模的尺寸可按照凹模的刃口尺寸配單面間隙
61、0.03~0.05。 得 凸模尺寸 *尺寸按凹模修配,單面間隙0.158~0.182。 5.4.3 壓力的計(jì)算 切口的周長(zhǎng)L=18+5+18+5=46。 ∴切口模沖裁F=1.25Ltτ=16100N。 5.5 第四工位切削模1的相關(guān)計(jì)算 5.5.1基本尺寸計(jì)算 計(jì)算各部分的模具刃口尺寸: 將圖4中的尺寸按IT14精度等級(jí)轉(zhuǎn)化為標(biāo)準(zhǔn)尺寸 25+0.527+0.315.5+0.436.3+0.37.38+0.31.5+0.257.38+0.313.3+0.43, 沖孔時(shí)的基準(zhǔn)型面在凸模上,凸模的型面尺寸的計(jì)算公式為: D=(d+xΔ)-δ
62、 (5.4) 其中:d—沖孔零件的極限尺寸: ∴凸模各部分尺寸為: L1=25+0.750.52=25.39, L2=7+0.750.3=7.23, L3=15.5+0.750.43=15.82,L4=6.3+0.750.3=6.53, L5=7.38+0.750.3=7.61, L6=1.5+0.750.25=1.69, L7=7.38+0.750.3=7.61, L8=13.3+0.750.43=13.62, ∴根據(jù)(5.5),可將上述的尺寸轉(zhuǎn)化到凹模上。 5.5.2 尺寸轉(zhuǎn)換 由公式 轉(zhuǎn)化
63、后的尺寸為: D1=25.39-0.021, D2=7.23-0.015, D3=15.82-0.018, D4=6.62-0.015, D5=7.61-0.015, D6=1.69-0.01, D7=7.61-0.015, D8=13.62-0.018。 根據(jù)基本尺寸按IT6可查得凸模的制造偏差: +0.013,+0.013,+0.013,+0.009,+0.009,+0.006,+0.009,+0.011。 根據(jù)式(12)分別校核凸、凹模制造偏差: L1: 0.021+0.013﹦0.034﹥2(0.065-0.053) =0.024,需
64、要調(diào)整偏差。 取δ凹=0.62(Cmax-Cmin)=0.60.024=0.014, δ凸=0.42(Cmax-Cmin)=0.010。 L2:0.015+0.013﹦0.028﹥2(0.065-0.053) =0.024,需要調(diào)整偏差。 取δ凹=0.62(Cmax-Cmin)=0.60.024=0.014, δ凸=0.42(Cmax-Cmin)=0.010。 L3:0.018+0.013﹦0.031﹥2(0.065-0.053) =0.024,需要調(diào)整偏差。 取δ凹=0.62(Cmax-Cmin)=0.60.024=0.014, δ凸=0.42(Cmax-Cmin)=0.01
65、0。 L4:0.015+0.009﹦0.0024=2(0.065-0.053) =0.024,不需要調(diào)整偏差。 L5:0.015+0.009﹦0.024﹦2(0.065-0.053) =0.024,不需要調(diào)整偏差。 L6:0.010+0.006﹦0.016<2(0.065-0.053) =0.024,不需要調(diào)整偏差。 L7:0.015+0.009﹦0.0024=2(0.065-0.053) =0.024,不需要調(diào)整偏差。 L8:0.018+0.011﹦0.029﹥2(0.065-0.053) =0.024,需要調(diào)整偏差。 取δ凹=0.62(Cmax-Cmin)=0.60.0
66、24=0.014, δ凸=0.42(Cmax-Cmin)=0.010。[13] ∴凹模的尺寸為: D1=25.39-0.014, D2=7.23-0.015, D3=15.82-0.014, D4=6.62-0.015, D5=7.61-0.015, D6=1.69-0.01, D7=7.61-0.015, D8=13.62-0.014。 凸模的尺寸按凹模的型面尺寸配單面間隙0.03~0.05。 5.5.3 壓力計(jì)算 切口的周長(zhǎng)L=6.3+1.8+15.5+7.38+7.38+1.5+6=46 ∴切口模沖裁F=1.25Ltτ=16100N。 5.6 第五工位側(cè)方孔 5.6.1 基本尺寸計(jì)算 圖5.4 沖側(cè)孔模切削的尺寸 零件的沖孔尺寸為113.5,在IT14精度等級(jí)下的標(biāo)準(zhǔn)尺寸為11-0.433.5-0.3,落料的基準(zhǔn)在凹模上,所以凹模的型面工作尺寸為: 凸模尺寸: Lp=(L+
- 溫馨提示:
1: 本站所有資源如無(wú)特殊說(shuō)明,都需要本地電腦安裝OFFICE2007和PDF閱讀器。圖紙軟件為CAD,CAXA,PROE,UG,SolidWorks等.壓縮文件請(qǐng)下載最新的WinRAR軟件解壓。
2: 本站的文檔不包含任何第三方提供的附件圖紙等,如果需要附件,請(qǐng)聯(lián)系上傳者。文件的所有權(quán)益歸上傳用戶所有。
3.本站RAR壓縮包中若帶圖紙,網(wǎng)頁(yè)內(nèi)容里面會(huì)有圖紙預(yù)覽,若沒(méi)有圖紙預(yù)覽就沒(méi)有圖紙。
4. 未經(jīng)權(quán)益所有人同意不得將文件中的內(nèi)容挪作商業(yè)或盈利用途。
5. 裝配圖網(wǎng)僅提供信息存儲(chǔ)空間,僅對(duì)用戶上傳內(nèi)容的表現(xiàn)方式做保護(hù)處理,對(duì)用戶上傳分享的文檔內(nèi)容本身不做任何修改或編輯,并不能對(duì)任何下載內(nèi)容負(fù)責(zé)。
6. 下載文件中如有侵權(quán)或不適當(dāng)內(nèi)容,請(qǐng)與我們聯(lián)系,我們立即糾正。
7. 本站不保證下載資源的準(zhǔn)確性、安全性和完整性, 同時(shí)也不承擔(dān)用戶因使用這些下載資源對(duì)自己和他人造成任何形式的傷害或損失。
最新文檔
- 2024《增值稅法》全文學(xué)習(xí)解讀(規(guī)范增值稅的征收和繳納保護(hù)納稅人的合法權(quán)益)
- 2024《文物保護(hù)法》全文解讀學(xué)習(xí)(加強(qiáng)對(duì)文物的保護(hù)促進(jìn)科學(xué)研究工作)
- 銷售技巧培訓(xùn)課件:接近客戶的套路總結(jié)
- 20種成交的銷售話術(shù)和技巧
- 銷售技巧:接近客戶的8種套路
- 銷售套路總結(jié)
- 房產(chǎn)銷售中的常見問(wèn)題及解決方法
- 銷售技巧:值得默念的成交話術(shù)
- 銷售資料:讓人舒服的35種說(shuō)話方式
- 汽車銷售績(jī)效管理規(guī)范
- 銷售技巧培訓(xùn)課件:絕對(duì)成交的銷售話術(shù)
- 頂尖銷售技巧總結(jié)
- 銷售技巧:電話營(yíng)銷十大定律
- 銷售逼單最好的二十三種技巧
- 銷售最常遇到的10大麻煩
相關(guān)資源
更多